Durch Aufkohlen, das auch als Carburieren oder Einsetzen bezeichnet wird, kann man den Kohlenstoffgehalt von Stählen erhöhen, die aufgrund eines zu geringen Gehalts nur schlecht oder gar nicht zum Härten geeignet sind.
Beim Aufkohlen werden diese Stähle mit Kohlenstoff angereichert, zumeist nur in der Randschicht. Dadurch bildet sich in der Randschicht mehr Martensit aus, sodass diese härter ist als der Kern des Werkstoffs. Dies ist beabsichtigt, da der Kern des Werkstücks in den meisten Fällen weich und zäh bleiben soll.
Das Aufkohlen stellt in der Regel die erste Phase des Einsatzhärtens dar. Bei diesem Härteverfahren für Stähle folgt auf das Aufkohlen, das Härten, Abschrecken und Anlassen. Derart behandelte Werkstoffe weisen eine harte, widerstandsfähige Oberfläche auf, besitzen jedoch einen weichen Kern. Vor allem die sogenannten Einsatzstähle werden mit diesem Verfahren behandelt.
Im Folgenden werden die unterschiedlichen Verfahren des Aufkohlens mit Aufbau und Funktionsweise beschrieben.
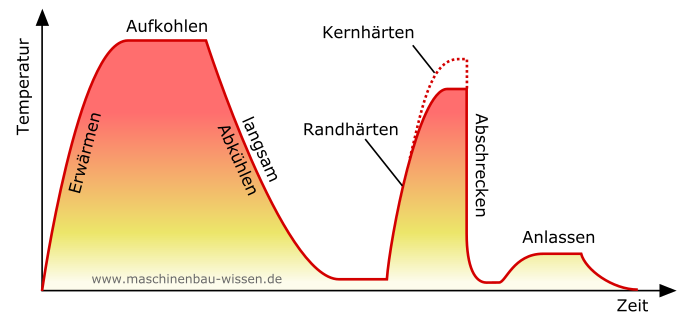
Ablauf des Verfahrens Einsatzhärten mit Aufkohlen
Aufkohlungsmittel für Stahl
In der Praxis werden unterschiedliche Aufkohlungsmittel verwendet:
Feste Aufkohlungsmittel
Feste Aufkohlungsmittel sind Granulate oder Pulver. Mit diesen werden die aufzukohlenden Werkstücke in geschlossene Kästen gesetzt und anschließend über eine vordefinierte Zeit bei einer Temperatur von etwa 930°C gehalten. Das Aufkohlen in Feststoffen wird heute kaum mehr angewandt. Ausschließlich Betriebshärtereien und einige wenige Lohnhärtereien führen dieses Verfahren nach wie vor durch. Der Grund liegt in der schlechten Reproduzierbarkeit der Ergebnisse. Zudem können durch die Verwendung von neuem Granulat bei der Aufkohlung Gefügefehler in der zu härtenden Schicht entstehen, diese resultieren aus einer Überkohlung (Korngrenzenzementit). Daher sollte neues Aufkohlungsgranulat stets mit altem vermischt werden.
Flüssig:
Hierbei werden die aufzukohlenden Teile in eine Salzschmelze eingesetzt und bei Temperaturen von 860 bis 950°C behandelt. Die hierfür verwendeten Aufkohlungssalze sind cyanidhaltig.
Vorteile der Aufkohlung im Salzbad sind die kurzen Prozesszeiten und die geringen Form- und Maßänderungen durch hängende Chargierung. Diese Art der Aufkohlung wird vor allem eingesetzt für geringe Aufkohlungstiefen von bis zu 0,4 mm. Indem die Konzentrationen von Kaliumcyanid und Kaliumcyanat im Salzbad ständig überwacht werden, kann eine optimale Reproduzierbarkeit des Aufkohlungsergebnisses gewährleistet werden. Die Konzentrationen werden durch Titration bestimmt. Da das Salzbadcarburieren aus ökologischer Sicht bedenklich und zudem relativ unwirtschaftlich ist, wird es heute nur noch in Einzelfällen durchgeführt.
Gasförmig:
Bei dieser Verfahrensart werden die aufzukohlenden Teile in gasförmige, kohlenwasserstoffhaltige Medien eingesetzt. Dann wird eine Aufkohlungsatmosphäre erzeugt. Diese besteht aus einem leicht reduzierenden Trägergas besteht sowie einem Anreicherungsgas, das dem Prozess kontrolliert zugeführt wird. Als Trägergas kommt in den meisten Fällen ein Gemisch aus 20 % Kohlenmonoxid, 40 % Wasserstoff und 40 % Stickstoff zu Einsatz. Als Anreicherungsgase bieten sich die Kohlenwasserstoffe Methan und Propan an. Das Aufkohlen im gasförmigen Medium ist die am weitesten verbreitete Methode.
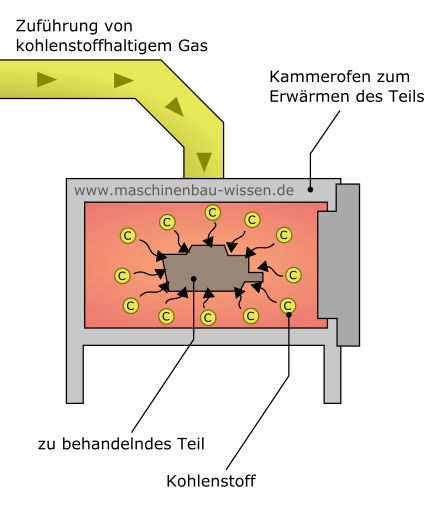
Aufbau und Funktionsweise des Verfahrens Aufkohlen / Einsetzen
Aufkohlen von Stahl über die Gasphase:
Beim Aufkohlen über die Gasphase gemäß Boudouard-Gleichgewicht handelt es sich um ein spezielles, aber mittlerweile veraltetes Verfahren.
Niederdruck:
Beim Niederdruck-Aufkohlen werden die aufzukohlenden Teile in einen Vakuum-Ofen eingesetzt. Beim Niederdruckaufkohlen gehen große Mengen an Kohlenstoff auf das Werkstück über. Daher wird der Prozess in Aufkohlungs- und Diffusionszyklen geteilt. Während der Aufkohlungszyklen verwendet man Kohlenwasserstoffe wie Methan und Propan um eine Aufkohlungsatmosphäre bei Drücken von 2 bis 25 Millibar zu erzeugen. In den Diffusionszyklen wird dem Ofen kein Kohlenstoffspender mehr zugeführt. Stattdessen wird der Druck abgesenkt und der Ofen in einigen Fällen mit Inertgasen bei geringem Druck gespült.