Konstruktion & Entwicklung - Skript
In diesem Skript geht es um das Thema Risikobeurteilung, Risikoanalyse und Gefährdungsbeurteilung. Die Risikobeurteilung für Maschinen und Anlagen wird durch einschlägige Richtlinien wie die Maschinenrichtlinie 2006/42/EG und entsprechend in nationales Recht umgesetzte Gesetze (z. B. Produktsicherheitsgesetz) zwingend erforderlich. Es handelt sich bei der Risikobeurteilung um ein spezielles Feld des Risikomanagements. Begriffe, die oft als Synonym für die Risikobeurteilung verwendet werden, sind Risikoanalyse, Gefahrenanalyse oder auch Gefährdungsbeurteilung.
Ziel ist immer die Risikominderung, was so viel bedeutet, dass man die vorhandenen Risiken soweit reduziert, bis lediglich ein tolerierbares Restrisiko bleibt. Die Risikominderung wird durch unterschiedliche Maßnahmen erreicht wie z.B. Lichtschranken, trennende Schutzeinrichtungen, Komponenten mit höherer Lebensdauer, zweikanalige Sensorik und andere Maßnahmen. Gestaltungsleitsätze werden auch in der Norm DIN EN ISO 12100:2010 "Sicherheit von Maschinen" vermittelt. Auch andere Normen beschreiben das Verfahren der Risikobeurteilung und geben Hilfe bei der Konstruktion sicherer Maschinen und Anlagen.
Weitere Informationen finden Sie auch auf unserer Partnerseite: Maschinen-Sicherheit.net
Dies ist eine Online-Anleitung, in der beschrieben wird wie man eine Risikobeurteilung bzw. eine Risikoanalyse erstellen kann. Dabei wird das schrittweise vorgehen entsprechend Norm gezeigt.
Begriffsklärung: Risikobeurteilung / Risikoanalyse
Bei der Risikoanalyse und Risikobeurteilung handelt es sich um ein eigenes Feld im Bereich des Risikomanagements (Risk Management). Rechtlich erforderlich wird die Risikoanalyse aufgrund diverser Richtlinien und Gesetze. Zu diesen Schriften zählen die Maschinenrichtlinie 2006/42/EG, Druckgeräterichtlinie 97/23/EG, die DIN 12100 oder auch das Produktsicherheitsgesetz. Doch auch aus eigenem Interesse des Maschinenentwicklers und Maschinenbetreibers sollte eine Risikobeurteilung erstellt werden. Denn die Sicherheit am Arbeitsplatz ist ein hohes Gut.
In der Grundnorm DIN EN ISO 12100:2010 (Sicherheit von Maschinen) findet man Gestaltungsleitsätze und Begriffsdefinitionen, die bei der sicheren Anlagen-Konstruktion helfen. Es wird darin auch beschrieben, wie man eine Risikoanalyse erstellen kann.
Anleitung- Risikobeurteilung erstellen
Zur Risikobeurteilung gehört das komplette Verfahren der Risikominderung*. Das Verfahren der Risikoanalyse und Risikobeurteilung gliedert sich in folgende Schritte:
- Bestimmung der Grenzen der Maschine oder Anlage
- Identifizierung der Gefährdungen / Risiken
- Risikoabschätzung
- Risikobewertung
- Risikominderung
Dabei kann die Risikobeurteilung bereits nach dem vierten Schritt enden, falls die Maschine bzw. die jeweilige Funktion bereits als sicher betrachtet wird. Falls die Funktion als nicht genügend sicher bewertet wurde, muss eine Risikominderung erfolgen. Dies geschieht anhand geeigneter Maßnahmen.
Die folgende Grafik veranschaulicht das Vorgehen beim Erstellen einer Risikoanalyse:
Ablauf einer Risikoanalyse und –bewertung
-
Bestimmung der Grenzen der Maschine oder Anlage
Zur Erstellung einer Risikoanalyse muss man als Erstes die Grenzen der Maschine festgelegen. Dies bezieht sich natürlich immer nur auf die Maschine, die bewertet werden soll. Die Grenzen der Maschine können dabei jedoch weiter ausgedehnt sein, als man im ersten Ansatz vermuten möchte.
-
Identifizierung der Gefährdungen / Risiken
Im Zweiten Schritt der Risikoanalyse geht es um die Identifizierung der Gefährdungen. Hierzu nimmt man am besten die verschiedenen Tätigkeiten und die damit verbundenen Aufgaben in Augenschein. Es werden bei der Identifizierung der Gefährdungen sämtliche Lebensphasen der Maschine betrachtet – d.h. von der Herstellung bis zur Stilllegung.
-
Risikoabschätzung
Nach der Identifizierung der Gefährdungen, folgt die Risikoeinschätzung. Diese wird im Rahmen der Risikoanalyse für jede Gefährdung durchgeführt, die zuvor identifiziert wurde. Dabei werden das Schadensausmaß, die Eintrittswahrscheinlichkeit und die Vermeidbarkeit abgeschätzt. Mit der Risikoabschätzung ist das Erstellen der Risikoanalyse abgeschlossen. Die restlichen Schritte zählen zum Bereich der Risikobewertung.
-
Risikobewertung
Nach der Risikoabschätzung folgt unmittelbar die Risikobewertung. Beim Erstellen der Risikobewertung* muss geprüft werden, ob das Risiko für die jeweilige Gefährdung hinreichend gemindert wurde, oder ob weitere Maßnahmen zu Risikominderung erforderlich sind. Ergibt die Risikobewertung, dass ein Risiko hinreichend gemindert wurde, dann endet damit das Verfahren der Risikobeurteilung für das jeweilige Risiko.
Erstellung einer Risikobeurteilung & Risikobewertung
-
Risikominderung
Wenn die Risikobewertung ergibt, dass das Risiko für die betrachtete Gefährdung noch nicht ausreichend gemindert wurde, werden weitere Maßnahmen zur Risikominderung erforderlich. Diese Maßnahmen müssen definiert werden, um danach das Risiko erneut zu bewerten.
Erste wenn das Risiko ausreichend verringert wurde, kann das Verfahren der Risikobeurteilung für die jeweilige Gefährdung abgeschlossen werden. Die 5 Schritte, mittels der wir die Risikobwertung und Risikoanalyse* erstellen, werde solange wiederholt, bis das Risiko gering genug ist. Was danach bestehen bleibt, wird als das vertretbare Restrisiko bezeichnet.
In diesem Artikel wird Ihnen der Risikograph für die Erstellung einer Risikoanalyse erläutert. Der Risikograph ist im Grunde ein Instrument oder besser gesagt eine Art Diagramm, das im Maschinenbau zur Bewertung von Risiken und Gefahren verwendet wird.
Der Risikograph
Bis zum Ende der 1970er Jahre existierten spezifische Sicherheitsmaßnahmen für jede Anlage oder Maschine, die zur Verbesserung der Sicherheit vorgeschrieben oder empfohlen waren. Es fehlte jedoch ein exakt beschriebener Zusammenhang zwischen der eingesetzten Technik, ihrer potenziellen Gefährdung und ihres realen Risikos. Erst Anfang der 80er Jahre konnte sich eine einheitliche Sichtweise der Sicherheitsmaßnahmen etablieren.
Innerhalb dieser Sichtweise werden genaue organisatorische oder technische Forderungen anhand des zu erwartenden Risikos einer Anlage oder Maschine* erstellt, die eine einheitliche Gefahrenminderung bewirken. Mittels der Bewertung einer Wahrscheinlichkeit, in der das zu erwartende Schadensausmaß (S) und die zu erwartende Häufigkeit (H) des Eintritts einer Gefahrensituation berücksichtigt werden, ergibt sich dabei das Risiko (R). Daraus wird die Höhe des Risikos nach folgender Formel berechnet:
R = H · S
Ein sehr bewährtes Verfahren, um Risiken bewerten zu können, ist der Risikograph, unabhängig vom Maschinentyp. Er hilft den Konstrukteuren dabei, geeignete Maßnahmen zur Einhaltung von Sicherheitsstandards zu finden.
Der Risikograph
Risikograph EN 954-1 (zurückgezogen und nicht mehr gültig):
Auch wenn der Risikograph aus der Norm EN 954-1 in der Literatur noch häufig anzutreffen ist, so sollten Sie diesen nicht verwenden, da die Norm zurückgezogen wurde.
Risikograph EN ISO 13849:
Um Risiken bewerten zu können, gibt es einen aktuell gültigen Risikographen aus der Norm EN ISO 13849.
Mit dem Risikographen Risiken bewerten
Mit diesen Risikographen erfolgt die Einstufung eines Risikos über die folgenden Bewertungskriterien:
- S: Ausmaß der Gefahr, des Schadens oder der Verletzung
- F (frequency): Häufigkeit des Auftretens
- P (probability): Möglichkeit zur Vermeidung oder Ausweichen der Gefahr
Die Höhe des jeweiligen Risikos ist abhängig davon, welche Verletzungen oder Schäden auftreten können, wie häufig dabei eine Person dieser Gefahr ausgesetzt wird und von der Möglichkeit, wie sie dieser Gefahr entkommen kann.
Wer Risiken bewerten möchte, muss für die allererste Risikobeurteilung die Anlage oder Maschine ohne jegliche Schutzeinrichtungen betrachten. Die Bewertung der Gefahr beginnt beim Startpunkt und führt entlang der Pfade des Risikographen hindurch, bis hin zu einer der Kategorien a bis e. Die entsprechende Kategorie gibt die Höhe des Risikos an. Dieser Rang des Risikos nennt sich auch Performance Level (PL), der angibt, wie hoch die Sicherheitsmaßnahmen sein müssen, mit denen das entsprechende Risiko minimiert wird.
Die Auswahl der Bauteile für eine Anlage oder Maschine richtet sich demnach nach dem ermittelten Performance Level aus dem Risikographen. Diesen PL-Wert müssen die Bauteile auf jeden Fall erreichen. Mit der Norm ISO 13849 sind mehrere Wege erlaubt, im Gegensatz zur früheren Norm EN 954-1. Deshalb können Sie geeignete Maßnahmen kombinieren, ohne die vordefinierten Sicherheitsstrukturen aus den Augen zu verlieren. Das heißt, wenn Sie Risiken bewerten*, dient Ihnen der Risikograph stets als Grundlage.
Die Risikominderung ist ein essentieller Schritt innerhalb einer Risikobeurteilung. Ziel ist hierbei die Reduzierung des Gefahrenpotentials einer Anlage oder Maschine auf ein vertretbares Restrisiko. Die Risikominderung wird immer dann notwendig, wenn die Risikobewertung zutage fördert, dass die betrachtete Anlage / Maschine noch nicht ausreichend sicher ist.
Zeigt die Risikobewertung jedoch, dass bereits eine genügende Sicherheit vorhanden ist und ein geringer Performance-Level als Bewertungsergebnis vorliegt, sind selbstverständlich keine Risikominderungsmaßnahmen erforderlich.
Sicherheit ist beim Entwerfen und Gestalten von Maschinen
Sicherheit ist beim Entwerfen und Gestalten von Maschinen eine integrale Anforderung. Der fortschreitende Innovationsprozess eröffnet nicht nur neue Möglichkeiten in Produktivität und Effizienz einer Maschine. Auch entstehen durch neue Technologien Gefahren, die vormals noch unbekannt waren. Außerdem ermöglichen neue Technologien auch erweiterte Sicherheitskonzepte.
Um auch in Zukunft Maschinen so sicher wie möglich gestalten zu können, wurde die bis 2007 gültige EN 954 durch die DIN 13894 abgelöst. Sie besteht aus zwei Teilen: Teil 1 beschreibt die allgemeinen Grundsätze, die zur sicheren Gestaltung einer Maschine gefordert werden. Teil 2 beschreibt die Prüfung vorhandener oder neu entwickelter Maschinen in Bezug auf ihre Sicherheit. Gestaltung und Prüfung sind dabei in einer Anleitung in aufeinander aufbauenden Stufen formuliert.
3-Stufen-Methode der Risikominderung
Die Sicherheit einer Maschine ist lt. DIN 31000, DIN 820-120, EN ISO 12100-1 und die EG-Maschinenrichtlinie 2006/42/EG nach einem dreistufigen Konzept der Risikominderung in der Konstruktion einzubeziehen.

Ablauf einer Risikobeurteilung mit Risikominderung
1. Stufe der Risikominderung = inhärent sichere Konstruktion
Die erste Stufe der Risikominderung ist die inhärent sichere Konstruktion. Dabei handelt es sich um konstruktive Maßnahmen, die von vorneherein eine Verhinderung einer potentiellen Gefährdungssituation darstellen. Dabei dürfen jedoch keine trennenden oder nichttrennenden Schutzeinrichtungen eingesetzt werden.
Diese Risikominderungsmaßnahmen wird am Beispiel von Hebebühnen deutlich: Eine Scherenarbeitsbühne, deren Mechanik mit einer Gewindeschraube betätigt wird, ist zwar langsam. Ein plötzlicher Ausfall des Hebemechanismus ist bei dieser Konstrukionsweise - im Gegensatz zu seilzugbetätigten Lösungen oder pneumatischen bzw. hydraulischen Systemen, aber ausgeschlossen.
2. Stufe der Risikominderung = technische sowie andere Schutzmaßnahmen
Die zweite Stufe ist die Abschirmung potentieller Gefahrenquellen mit Hilfe von trennenden oder nichttrennenden Schutzeinrichtungen oder auch anderen technischen Schutzmaßnahmen.
Am Beispiel der Scherenarbeitsbühne wurde zwar der Ausfall des Hebemechanismus konstruktiv ausgeschlossen. Dafür sind aber entlang der Hebemechanik zahlreiche Gefahrenstellen, bei denen man sich beispielsweise die Finger einklemmen kann. Hier können Schutzbleche ein Eingreifen verhindern.
3. Stufe der Risikominderung = Benutzerinformationen
Die dritte Stufe sieht als Risikominderungsmaßnahme die Information der Benutzer der Anlage bzw. der Maschine vor. Diese Benutzerinformation kann durch die Anbringung von Warnschildern realisiert werden, aber auch durch Sicherheitshinweise Piktogramme, Kennzeichnungen, Warneinrichtungen und Signale.
Ist eine Gefahrenquelle konstruktiv nicht auszuschließen oder nicht wirksam abzuschirmen, muss vor ihr mit eindeutig zuordenbaren Hinweisen gewarnt werden. Die Gefahrenstellen müssen auch in der Betriebsanleitung der Maschine benannt werden.
Seit 1995 müssen im Europäischen Wirtschaftsraum in Verkehr gebrachte Maschinen die Anforderungen der Richtlinien 2006/42/EG erfüllen, die eine Risikobeurteilung im Entwicklungsprozess der Maschine beinhaltet. Die Bewertung und Einstufung von sicherheitsgerichteten Funktionen der Maschine erfolgt über die Berechnung des Performance Levels (PL)*, der durch die harmonisierte Sicherheitsnorm EN ISO 13849-1 erforderlich wird und eine wichtige Kenngröße ist. Diese Norm löste die EN 954 im September 2009 vollständig ab. Im Folgenden erfahren Sie, wie der Performance Level zu berechnen ist.
Der Performance Level (PL) und seine Bedeutung
In der Norm EN ISO 13849 wird der Performance Level als diskreter Level beschrieben, mit dem die Fähigkeit von sicherheitsbezogenen Teilen eines Bauteils oder einer Steuerung spezifiziert wird, damit eine bestimmte Sicherheitsfunktion unter vorhersehbaren Bedingungen ausgeführt werden kann. Da bedeutet, dass der Performance Level als Maß für die Zuverlässigkeit einer Sicherheitsfunktion fungiert. Dabei ist der Performance Level auf einer Skala, ausgehend vom geringsten PL (a) bis zum höchsten PL (e), zu ermitteln.
Die Sicherheit eines Bauteils oder einer Funktion einer Maschine wird mithilfe des PL bewertet und entsprechend angegeben. Je höher der PL der Funktion ist, desto zuverlässiger und sicherer ist sie. Somit hat der ermittelte Wert für den PL eine Auswirkung auf die Einsatzmöglichkeit des Bauteils. Der PL des betrachteten Bauteils muss dabei mindestens so hoch sein wie der Risikowert der betrachteten Funktion. Das heißt, wenn sich für eine Funktion beispielsweise ein Risikowert c ergibt, darf der PL des Bauteil auch nur bei c oder höher (d oder e) liegen.
Den Performance Level PL berechnen
Es sind immer zwei Performance Level zu ermitteln
Für die Sicherheitsauslegung einer Anlage oder Maschine nach der Norm EN ISO 13849 sind stets zwei PL zu berechnen, und zwar der erreichte Performance Level (PL) und der erforderliche Performance Level (PLr).
Erreichter Performance Level (PL):
Zum Berechnen des PL werden der Aufbau der Steuerung oder der Aufbau der Sicherheitsbauteile und die jeweilige Gefährdungssituation betrachtet. Dabei kommt es auf die MTTF-Werte (engl. Mean Time To Failure = mittlere Zeit bis zum Gefahr bringenden Ausfall), auf den Diagnosedeckungsgrad (DC) sowie auf die Steuerungskategorien (B, 1, 2, 3, 4) an, die unter anderem von der Steuerungsarchitektur abhängen.
Erforderlicher Performance Level:
Der erforderliche Performance Level ergibt sich aus den Parametern: Ausmaß der Gefahr, des Schadens oder der Verletzung, Häufigkeit des Auftretens und Aufenthaltsdauer sowie Möglichkeit zur Vermeidung oder Ausweichen der Gefahr. Daraus ist zum Schluss der Bewertung der PLr zu ermitteln. Die Beurteilung nach EN ISO 13849 erfolgt dabei ähnlich wie die Risikobeurteilung nach EN 954-1.
Ermittlung des PLr:
Der erforderliche PLr wird meist mit einem relativ einfachen Diagramm ermittelt, das auch als Risikograph bekannt ist. In diesem Diagramm wird ein Risiko für ein bestimmtes Bauteil oder eine bestimmte Funktion anhand der oben schon erwähnten Parameter bewertet:
- Ausmaß der Gefahr, des Schadens oder der Verletzung: S1 für leichte Verletzungen, S2 für schwere Verletzungen
- Häufigkeit des Auftretens und Aufenthaltsdauer: F1 für selten bis öfter, F2 für häufig bis dauernd
- Möglichkeit zur Vermeidung oder Ausweichen der Gefahr: P1 für möglich unter bestimmten Bedingungen, P2 für kaum möglich
Bestimmen des PLr mit dem Risikographen:
Durch das Verfolgen der entsprechenden Pfade im Diagramm (Risikographen) kann der PLr ermittelt werden, der entweder a, b, c, d oder e sein kann und den die untersuchte Funktion mindestens erreichen muss.
Mit der entsprechenden Software ist das Verfahren natürlich einfacher. SISTEMA ist zum Beispiel ein kostenloses Software-Tool zur Berechnung der Performance Level.
In diesem Tutorial wird Ihnen gezeigt, wie Sie den MTTF-Wert berechnen können, der bei der Risikobeurteilung nach der Norm EN ISO 13849 erforderlich ist.
Der MTTF-Wert:
Der Begriff MTTF gehört zum Bereich der Gefährdungsbeurteilung und Risikoanalyse*. Seine genaue Bedeutung ist "Mean Time To Failur" (abgekürzt MTTF). Das bedeutet auf Deutsch so viel wie "mittlere Betriebsdauer bis zum Ausfall". Demnach gibt der MTTF-Wert die mittlere Lebensdauer einer Komponente an.
Der MTTF-Wert hat erst mit der Norm EN ISO 13849-1 eine besonders hohe Bedeutung bekommen, da entsprechend dieser Norm der Performance Level auf Basis des MTTF-Wertes ermittelt werden kann. Demnach ist der MTTF-Wert sehr wichtig für die Risikobewertung von Anlagen und Maschinen. Ebenso ist er ein wichtiger Faktor für die CE-Kennzeichnung, da die Maschinensicherheit auch innerhalb der Konformitätsuntersuchungen bewertet wird.
Der MTTFd -Wert:
Zur Ermittlung des Risikos ist auch der MTTFd -Wert (ausgeschrieben: "Mean Time To Dangerous Failure") von Bedeutung, bei dem es sich um die "Mittlere Zeit bis zum Gefahr bringenden Ausfall" handelt. Der MTTFd -Wert von technischen Schutzmaßnahmen wird entsprechend der Norm DIN EN 13849-1 in drei Bereiche unterteilt: niedrig, mittel und hoch. (Siehe Tabelle unten.)
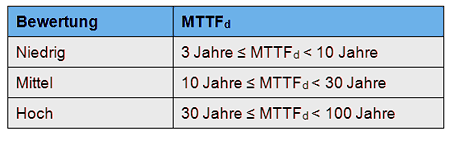
Quelle DIN EN ISO 13849-1 Kapitel 4.5.2
Ermittlung des MTTFd -Wertes für eine Sicherheitsfunktion
Ermittlung des MTTFd -Wertes für mechanische Komponenten:
Zur Berechnung des MTTFd - Wertes für mechanische Komponenten findet der sogenannte B10d-Wert Verwendung, der die nominale Lebensdauer der entsprechenden Komponente bezeichnet. Bei diesem Wert handelt es sich um die mittlere Anzahl von Schaltspielen, nach denen bis zu 10% der jeweils betrachteten Einheiten gefahrbringend ausfallen.
Ermittlung des MTTFd -Wertes für elektronische Komponenten:
MTTFd -Wert für einen Kanal:
Für die Berechnung des MTTFd -Wertes von elektronischen Sicherheitsfunktionen mit nur einem Kanal dient folgende Formel:
MTTFd-Wert für zwei redundante Kanäle:
Es existieren ebenso Methoden zur Berechnung des MTTFd -Wertes von Sicherheitsfunktionen mit zwei Kanälen (Redundanz). Jeder Entwickler kann diese Methoden selbst anwenden. Um den Gesamt- MTTFd -Wert ermitteln zu können, wird zuvor jeder redundante Kanal einzeln berechnet. Der Gesamt- MTTFd -Wert ergibt sich anschließend aus folgender Formel:
Dieser ermittelte Gesamt- MTTFd -Wert ist ein qualitativer Wert der Sicherheitsfunktion* einer Komponente. Er wird in Jahren angegeben. Wichtig: Er gibt nicht die garantierte Lebensdauer an, da er als Teilaspekt zur Berücksichtigung der Güte der verwendeten Komponenten nur ein statistischer Wert ist.