Beim sogenannten Rotationsformen handelt es sich um ein besonderes Verarbeitungsverfahren von Kunststoff. Das Verfahren wird auch als Rotomolding bezeichnet. Wird thermoplastischer Kunststoff in Form von Pulver als Werkstoff verwendet spricht man alternativ auch vom Sinterrotieren oder Rotationssintern, während beim Einsatz von Gießharzen auch die Rede vom Schleudergießen ist.
Eine Besonderheit des Verfahrens ist, dass damit Hohlkörper aus Kunststoff hergestellt werden. Das Verfahrensprinzip sieht so aus, dass flüssiger Kunststoff oder Kunststoff-Pulver in einem rotierenden Werkzeug zu einem Bauteil geformt wird.
Verfahren Rotationsformen
Beim Rotomolding wird entweder ein Gießharz verwendet, das in das Formwerkzeug gegossen wird, oder ein Thermoplast-Pulver, das schichtweise in das Werkzeug eingebracht, verdichtet und durch Hitze aufgeschmolzen wird. Beim Rotationsformen mit Pulver ist auch vom Sinterrotieren oder Rotationssintern die Rede. Aufgrund der Rotation der Form wird der flüssige Kunststoff durch die Zentrifugalkraft an die Wand des Werkzeugs gedrückt und bildet diese nach dem Erstarren ab.
Gießharze werden kurz vor dem Vergießen z.B. aus Harz und Härter gemischt und erstarren durch chemische Reaktion. Thermoplastische Pulver werden in der Form durch Hitze aufgeschmolzen und Erstarren durch das anschließende Abkühlen auf Raumtemperatur. Nach dem Erstarren des Kunststoffs wird die Form geöffnet und das fertige Bauteil kann entformt werden.
Bei den Werkzeugen handelt es sich um dünnwandige Hohlkörperformen. Die Rotation des Werkzeugs kann entweder mit einer Rotationsache erfolgen oder auch durch biaxiale Rotation realisiert werden. Am Ende entstehen Bauteile mit relativ gleichmäßigen Wandstärken von 2 bis 15 mm.
Rotomolding-Anlagen
Die Anlagen, die für das Rotationsformen eingesetzt werden, können wie folgt unterteilt werden:
Einzelschussmaschinen:
Bei diesen Anlagen geschieht der Gesamtprozess Schritt für Schritt. Die Formen werden beschickt, erwärmt, aufgeheizt, gekühlt und das Bauteil entformt. Die Einzelschussanlagen haben den Vorteil, dass die Prozesszeit besser ausgenutzt wird. Sie weisen jedoch auch ein geringere Flexibilität auf, was die Herstellung unterschiedlicher Teilegrößen angeht und erfordern zudem einen höheren Platzbedarf.
Rock n‘ Roll-Anlagen:
Bei dieser Art von Rotomolding-Anlagen handelt es sich um Einzelschussanlagen, welche sich nur in der Hauptachse drehen. In der Nebenachse können sie lediglich eine Kippbewegung ausführen. Mit den Rock n‘ Roll-Anlagen werden in erster Linie zylindrische, längliche Teile hergestellt.
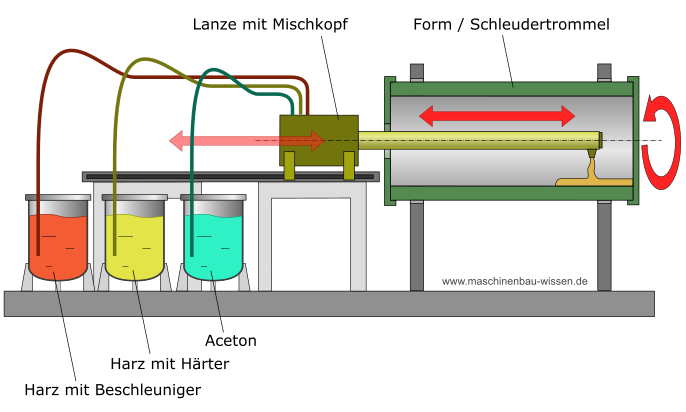
Aufbau einer Rotationsform-Anlage
Kunststoffe für das Rotationsformen
Für das Rotationsformen eingesetzt werden hauptsächlich
- Polyethylen (PE, auch elektrisch leitend) in Pulverform,
- Polypropylen (PP) in Pulverform sowie
- Gießharz z.B. Epoxidharz (flüssig)
Mit speziellen Einrichtungen an den Anlagen lassen sich auch fast alle weiteren Thermoplast-Produkte in Form von Pulver verwenden. Z.B.:
- Polyamid (PA),
- Polycarbonat (PC) und
- Polystyrol (PS).
Vorteile des Rotationsformens:
Im Vergleich zum Blasformen oder Spritzgussverfahren weist das Rotationsformen folgende Vorteile auf:
- Werkzeuge einfache und damit kostengünstig
- bereits für kleine und mittlere Serien von 20 bis 2.000 Stück/Jahr wirtschaftlich
- Hohlteile mit Volumen bis 6.000 Liter herstellbar
- Komplexere Geometrien abbildbar - Öffnungen, durchgehenden Verbindungen, Gewinden, Einlageteilen usw.
- gleichmäßige Wandstärken realisierbar
- nahtlose Hohlkörper herstellbar
Anwendung Rotationsformen
Einsatzgebiet des Verfahrens Rotationsgießen ist die Herstellung von Kunststoff-Hohlteilen. Es handelt sich hier typischer Weise um Tanks, Maschinen-Gehäuse, Freizeitartikel, Wassersportartikel wie Kajaks, Transportbehälter, Sicherheitsbehälter, Spielzeugteile und ähnliches. Aufgrund seiner vergleichsweise geringen Kosten für die Formwerkzeuge, wird das Rotationsformen gerade für kleine Serien bevorzugt eingesetzt.