Doppelschneckenextruder gehören zu den Mehrwellenextrudern und sind Maschinen, die in der Kunststofftechnik zur Verarbeitung von Thermoplasten eingesetzt werden. Sie werden in die Obergruppe der Extruder eingruppiert. Im Bereich der Kunststofftechnik dienen Sie der Aufbereitung sowie der Extrusion (Formgebung) von Kunststoff-Schmelzen. Das zu verarbeitende Polymer wird im Extruder mittels zwei rotierender Schneckenwellen längs durch einen beheizbaren Zylinder gefördert. Dabei wird das Material aufgeschmolzen.
Typischer Aufbau eines Doppelschneckenextruders für die Verwendung in der Kunststofftechnik
Das wichtigste Element im Hinblick auf die Verfahrenstechnik sind die beiden Schneckenwellen. Sie liegen in einem Zylinder, der mit einer achtförmigen Bohrung versehen ist und greifen ineinander. Vor allem Laborextruder sind im Sinne einer flexiblen Umrüstung aus einzelnen Modulen aufgebaut. Die Lagerung der Schnecken erfolgt einseitig. Sie sind entweder über eine Passfederverbindung oder eine Keilwellenverbindung mit der Getriebestufe verbunden, die sie antreibt. Das Extrudergetriebe wird in den meisten Fällen durch einen Elektromotor angetrieben.
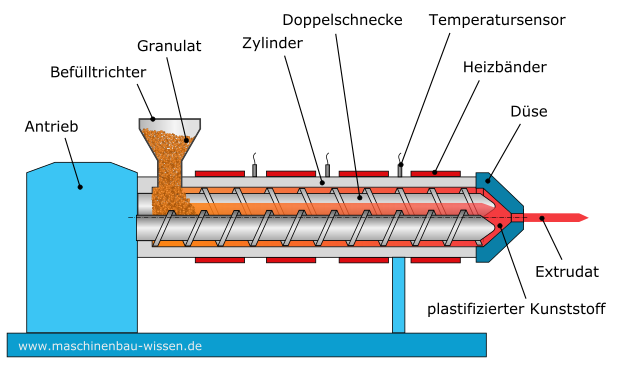
Aufbau eines Doppelschneckenextruders
Die thermoplastischen Materialien werden auf etwa 20°C über dem Schmelzpunkt des jeweiligen Materials aufgeheizt. Dies geschieht durch elektrische Heizpatronen oder mittels Heizschalen. Die Temperierung erfolgt pro Schuss, sodass dieser an die Prozessvorgaben angepasst werden kann. Die Gehäusekühlung des Zylinders erfolgt mittels Wasserkreisläufen, die durch Relaisschaltungen gesteuert werden. Dies dient der Vorbeugung der Überhitzung des Materials, die mit schädlichem Materialabbau einhergeht.
Die genannte Heizung und Kühlung wird jedoch nicht zur Aufschmelzung des Kunststoff-Materials genutzt. Sie dienen ausschließlich der korrekten Temperierung des Prozesses. Die Kunststoff-Aufschmelzung wird erreicht durch die Einleitung von Energie welche durch die Schneckendrehung erzeugt wird. Somit ist die Leistung des Antriebs wesentlich für die Aufschmelzung.
Unterschiedliche Bauformen des Doppelschneckenextruders
Man unterscheidet beim Doppelschneckenextruder unterschiedliche Bauformen. Die Unterscheidung wird anhand der Rotationsrichtung sowie des Achsabstandes zwischen den Schneckenwellen vorgenommen. Es gibt:
- tangierende Gleichdralldoppelschneckenextruder
- dichtkämmende Gleichdralldoppelschneckenextruder
- tangierende Gegendralldoppelschneckenextruder
- dichtkämmende Gegendralldoppelschneckenextruder
Bei Gegendralldoppelschneckenextrudern wird wenig Scherung ins Material eingebracht. Daher wird dieses wenig belastet. Sie kommen vor allem für die Extrusion von temperaturempfindlichem Kunststoff wie etwa PVC zum Einsatz. Die am weitesten verbreitete Bauform ist der dichtkämmende Gleichdralldoppelschneckenextruder. Auf ihn wird im Folgenden näher eingegangen.
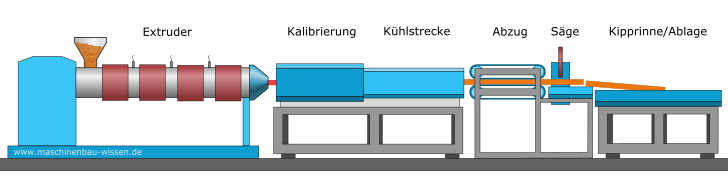
Aufbau einer kompletten Extrusionsanlage
Gestaltung der Schnecke
Die Planung der erforderlichen Prozessschritte beinhaltet unter anderem die Anpassung der Schneckengestaltung. Um unterschiedliche Aufgaben realisieren zu können, stehen dem Konstrukteur hierbei viele verschiedene Gestaltungsmöglichkeiten für die Schnecke zur Verfügung.
Die Verfahrenszonen beim Doppelschneckenextruder
Es können folgende Bereiche der Verfahrenstechnik über die Länge der Doppelschnecken beschrieben werden:
Die Einzugszone: In diesem Bereich wird das zu verarbeitende Material gefördert und eingezogen.
Die Aufschmelzzone: Diese Zone dient dem Aufschmelzen des Materials und es wird eine Vordispergierung von Füllstoffen und Ähnlichem vorgenommen.
Die Kompressionszonen: Aufgrund der kleiner werdenden Steigung der Doppelschnecken erfolgt eine Verdichtung des Materials. Hierdurch nimmt der Füllgrad im Schneckengang zu. Bei Vollfüllung steigt dadurch der Druck an und das Material ist bereit für die Extrusion.
Die Mischzonen: In die Schnecke können spezielle Mischelemente integriert sein. Dadurch lässt sich die Mischleistung erhöhen. Das ist insbesondere dann wichtig, wenn eine homogene Einmischung von Zuschlagstoffen gewünscht ist. Hierbei kann es sich zum Beispiel um Färbemittel, Ruß etc. handeln.
Die Entgasungszonen: In manchen Schmelzen sind flüchtige Bestandteile enthalten. Um diese zu entziehen, ist es wichtig, dass der Füllgrad im Schneckenzylinder unter 100 Prozent liegt. Ansonsten würde die Schmelze in den Entgasungsstutzen gedrückt.
Die Austragszone: Diese Zone ist notwendig, um den Druck aufzubauen, der notwendig ist, um den Fließwiederstand des Werkzeugs während er Extrusion zu überwinden.
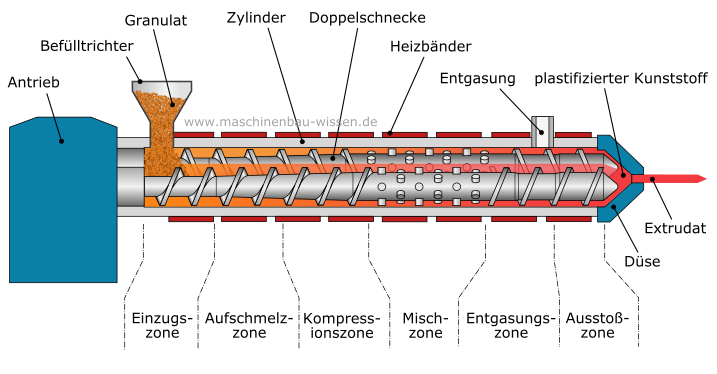
Zonen in einem Doppelschneckenextruder
Geometrische Beziehungen beim Doppelschneckenextruder
Die Förderwirkung des Doppelschneckenextruders beruht auf der Zwangsförderung. Am Zwickelpunkt wird die Schmelze von der abtreibenden Flanke der einen Schnecke an die auftreibende Flanke der anderen Schnecke übergeben. Dadurch entstehen stetig Strömungsumlagerungen und somit auch zu einer Scherung des Materials.
An der förderwirksamen Flanke im Einzugsbereich sind die Elemente der Schnecke abgeflacht, um die Förderleistung zu erhöhen. Man bezeichnet diese Elemente als Schubkantenelemente. Um die Mischung im Zylinder zu verbessern, setzt man Knetelemente und Zahnmischelemente ein. Wahlweise führt man diese entweder förderwirksam oder nicht förderwirksam aus.
Besonderheiten beim Doppelschneckenextruder
Der Doppelschneckenextruder ist deutlich teurer in der Herstellung als der Einschneckenextruder. Zum einen ist die Maschinentechnik kostenaufwendiger. Zum anderen sind Doppelschneckenextruder nur für ein begrenztes Einsatzgebiet verwendbar, wodurch auch nur geringere Stückzahlen hergestellt werden können. Die Schnecken müssen biegefest sein. Denn im Zwickelbereich sind sie hohen Belastungen ausgesetzt und werden nach außen gedrückt. Deswegen müssen sie in der Regel härter und verschleißfester sein als die Schnecken in einem Einschneckenextruder. Die achtförmige Bohrung im Zylinder sowie die Lagerung der Doppelschnecken sind ebenfalls sehr aufwendig zu fertigen.
Dafür jedoch entfaltet ein Doppelschneckenextruder eine deutlich bessere Mischwirkung als ein Einschneckenextruder. Sie bieten zudem eine sehr gute Entgasungsleistung und zeichnen sich durch eine gute Selbstreinigung aus.
Nahezu alle verfahrenstechnischen Teile sind im Doppelschneckenextruder hohem korrosivem und/oder abrasivem Verschleiß ausgesetzt. Daher ist die Auswahl geeigneter Materialen für die Doppelschnecken immens wichtig, um deren Standzeiten zu erhöhen und somit die Prozesskosten zu senken.